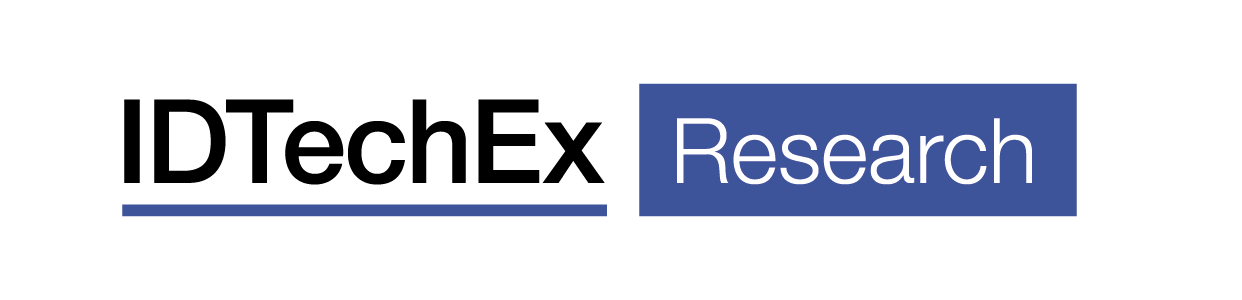
Author: Conrad Nichols, Technology Analyst at IDTechEx Variable renewable energy (VRE) penetration is expected to continue increasing across the globe, and with this will come increasing variability and uncertainty in energy and electricity supply. Energy storage systems will be needed to dispatch energy over longer timeframes when energy from VRE sources is not available. An example of one such technology is the redox flow battery (RFB). From IDTechEx’s market report, “Redox Flow Batteries Market 2024-2034: Forecasts, Technologies, Markets”, as the demand for such technologies will increase, so will the opportunities for players across the value chain to generate revenues. Upstream in the value chain, players will look to manufacture materials and components and supply these to RFB developers. Electrolyte A complete RFB system consists of three main components: the electrolyte, the cell stack, and balance of plant (BOP). The most widely deployed RFB system, the VRFB, uses expensive vanadium electrolyte. In 2021, 120,000 MT of vanadium was supplied by miners globally, with 92% of this going towards steel production, with the VRFB market accounting for 2%. A few key companies, such as Glencore, Largo, and Bushveld, are responsible for mining vanadium and will be key players in this part of the supply chain. Vanadium electrolyte comprises approximately 30-50% of the unit cost of a VRFB and will be influenced by the overall system size, as well as the duration of storage required. Cell stack The cell stack is also responsible for a reasonable portion of the unit cost of VRFBs and comprises several key components. This includes the membrane, bipolar plates, electrodes, gaskets, and sealants. The two arguably most expensive components of a VRFB cell stack are the membrane and bipolar plates. As RFB deployments continue to increase, so will the demand for components and materials that make up these systems.
|
||
Exploded RFB Cell Stack. Source: IDTechEx |
||
Membranes The role of membranes is that of preventing the two electrolytes in an RFB from mixing and the two electrodes from touching but, at the same time, allowing the flux of counter ions (like H+). Membranes typically have a trade-off between ionic conductivity and species selectivity. Commercially deployed membranes have thicknesses in the range of 50 – 200 microns. In an RFB, the ideal membrane should have good ionic exchange capacity and ionic conductivity, a low permeation of active species to prevent self-discharge and be chemically resistant to aggressive species. The most typically deployed membranes in RFBs are cationic ion exchange membranes (IEMs). Cationic IEMs are either fluorinated or non-fluorinated. The standard material for fluorinated cationic IEMs is perfluorosulfonic acids (PFSAs), with the main example of this branded material being “Nafion”, originally manufactured by DuPont. These have good ionic conductivity and resistance to acidic environments, though they have non-negligible vanadium species crossover rates in VRFBs. Some RFB developers, in interviews with IDTechEx, commented that they have focused their R&D efforts to reduce this and claim this is no longer a downside to their technology. However, these materials have remained confidential, as these are likely to give a commercial advantage. Therefore, it is expected cationic IEMs will remain the popular membrane choice for RFB systems, given their well-rounded properties. However, as highlighted in IDTechEx’s study, these are an expensive component of the cell stack, accounting for ~50% of the stack cost. Bipolar plates The bipolar plate increases the structural stability of the stack and allows the flux of electrons from the positive electrode of one half-cell to the negative electrode of the following half-cell. Materials typically used for bipolar plates are graphite, graphite-filled polymers, titanium, or steel. Binders can be used in composite bipolar plate manufacturing, and these are usually thermoplastics or thermoset polymers, e.g., fluoropolymers, polyethylene, and polypropylene. These typically form 10 – 20% of the bipolar plate material composition. Example players of bipolar plates include Hycco and Schunk. Ultimately, bipolar plates form a significant portion of the cell stack cost. Outlook Over the coming decade, it will be important that RFB manufacturers will have established their supply chains to meet growing demand for long duration energy storage technologies. There will be growing opportunities for players upstream in the value chain to supply materials and components to RFB developers. These could be for electrolyte, membranes, bipolar plates, or the materials that make these up, such as PFSAs, graphite, graphite-filled polymers, titanium, steel, thermoplastics, thermoset polymers, etc. While electrolyte accounts for ~30-50% of the unit cost of VRFBs, and the membrane and bipolar plates, combined, constitute most of the cell stack cost, suppliers of electrodes, gaskets, sealants and auxiliary components will also be key for supporting continued RFB market growth. For more information on RFB materials, players, value chains, technologies, economics, and granular 10-year RFB market forecasts, please refer to IDTechEx’s latest report “Redox Flow Batteries Market 2024-2034: Forecasts, Technologies, Markets”. To find out more about this report, including downloadable sample pages, please visit www.IDTechEx.com/Redox. To find out more about the energy storage market research available from IDTechEx, please visit www.IDTechEx.com/EnergyStorage. |
|