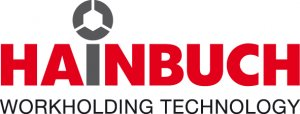
Hota Industrial is the largest manufacturer of drive components in Taiwan. The Taichung-based company now uses the Mando G211 mandrel from Hainbuch for the production of transmission parts for electric cars. The material used, a low-alloy case-hardening steel, and the monthly production volume of 20,000 units place high demands on machines and tools. The workholding manufacturer from Germany was able to meet the requirements, resulting in a 20 percent increase in productivity.
The collaboration between Hota and Hainbuch began in May 2021. The gear manufacturer planned to change the clamping situation for all process steps before hardening in order to achieve higher process reliability and production quality. The drive gears are manufactured on a Hartech HGH-250 gear hobbing machine. Hartech is the mechanical engineering division of the Hota Industrial Group. Previously, Hota used collets in the production of helical drive gears. “For our production, the collets did not meet the requirements for concentricity and repeatability,” says Alex Chao, Deputy Head of Design at Hota Industrial.
Convincing rigidity achieved
The selected Mando G211 mandrel clamps radially with pull-back effect. Depending on the mandrel size, the radial clamping force of the mandrel is 42 to 150kN. This extremely rigid I.D. clamping provides the required accuracy. Integrated flushing channels keep the clamping device free of chips. The improved process also reduces the machining time per part. The segmented clamping bushings of the mandrel are vulcanized and thus dampen vibrations during machining. The service life of the tools has increased significantly since the mandrel had been installed.
20 percent less set-up time
The service life of the mandrel Mando G211 is longer than that of the collets previously used. “The mandrel with the segmented clamping bushings offers high concentricity and also a long service life of the vulcanization,” says Chao, explaining the choice of clamping device.
The handling of the clamping devices has also been simplified for the user: the G211 with its slim tool runout contour is ideal for gear production. The maximum length of the mandrel is 213 mm. The vulcanized segmented clamping bushing also enables a span range from 0.5 mm (clamping range 20-28 mm) up to 0.9 mm (clamping range of the mandrel from 69-120 mm). This makes it easier to compensate for workpiece diameter tolerances during work preparation. The effect of changing to the mandrel from Hainbuch is a reduction in both set-up time and machining time by 20 percent.
Good service makes all the difference
Selecting the right workholding technology has significantly improved the entire production process. The advice provided by Hainbuch was also an important factor in Alex Chao's choice of the workholding manufacturer: “We are very satisfied with the service and advice provided by the Hainbuch employees,” confirms Chao. Compared to other manufacturer’s products, the Mando G211 mandrel impressed with its stability, service life and good price-performance ratio. In the future, Hota plans to introduce the Hainbuch Mando G211 as an option for all new machines.
About Hota Industrial
Hota Industrial was founded in 1966 and has grown from a small family-run workshop to become the largest manufacturer of power transmission components in Taiwan. With an annual production volume of 20 million components, Hota is a global leader in transmission production, with only 4% of products sold domestically and 96% exported to automotive manufacturers worldwide. Hartech is the mechanical engineering division of the HOTA Industrial Group, which has been responsible for the gear business as a separate division since 2023.
Images:
The Mando G211 mandrel clamps radially with a pull-back effect. Depending on the mandrel size, the radial clamping force of the mandrel is 42 – 150 kN.
The segmented clamping bushing of the Mando G211 mandrel is vulcanized and thus dampens vibrations during machining. The service life of the tools has increased since using the mandrel.
The Mando G211 mandrel with its slim tool run-out contour is ideal for gear production.